Environmental Testing of Intuition-1 Satellite
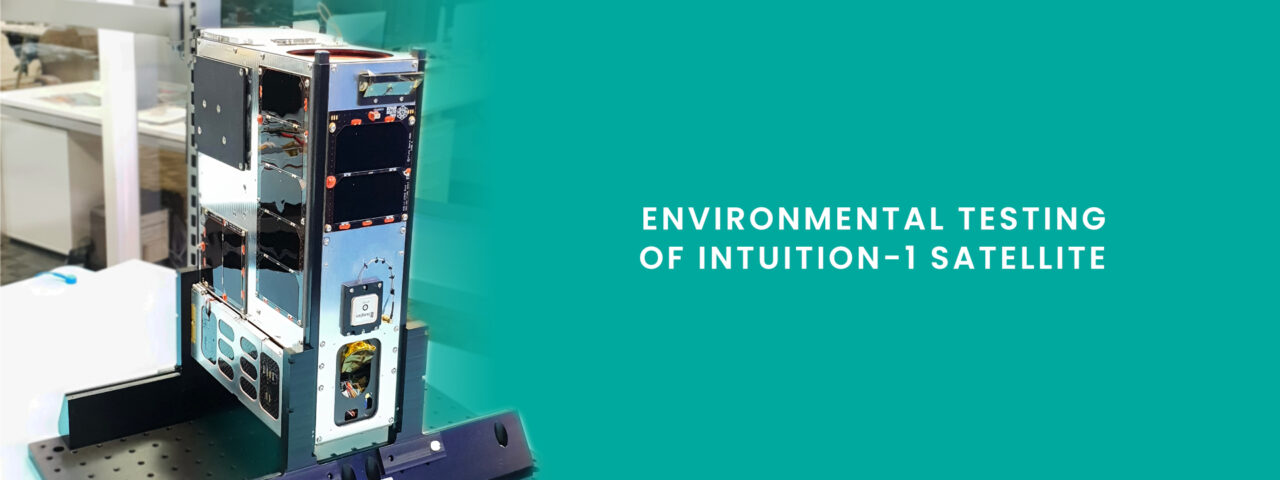
Intuition-1: From Assembly to Environmental Validation
In the previous article, the assembly process of the Intuition-1 spacecraft was detailed, highlighting the intricate integration of various components for optimal alignment. However, the crucial step of verifying component functionality was not touched upon. This entry delves into the environmental testing campaign of the Intuition-1 spacecraft.
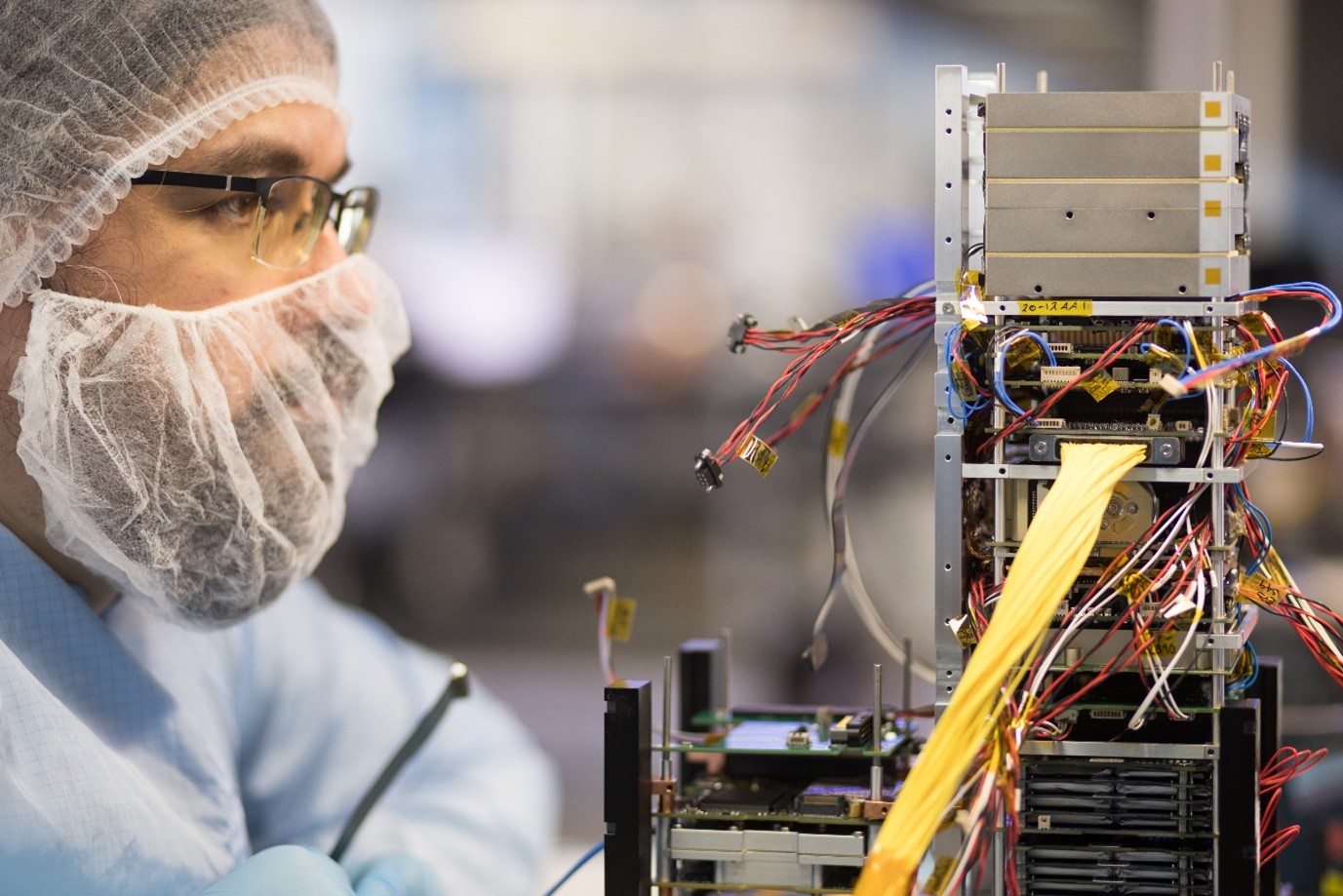
Integrating Leopard with Spacecraft platform, image courtesy of AAC Clyde Space.
Strategies in Spacecraft Testing
For spacecraft assembly and testing, various methodologies exist. For Intuition-1, a hybrid strategy was adopted. The entire spacecraft followed the ProtoFlight Model methodology, wherein tests were conducted on the specific unit destined for space launch. However, for KP Labs’ core components, the QM/FM model was utilized. This entailed conducting comprehensive environmental tests on the Qualification Model while the actual Flight Models underwent a selective suite of acceptance tests.
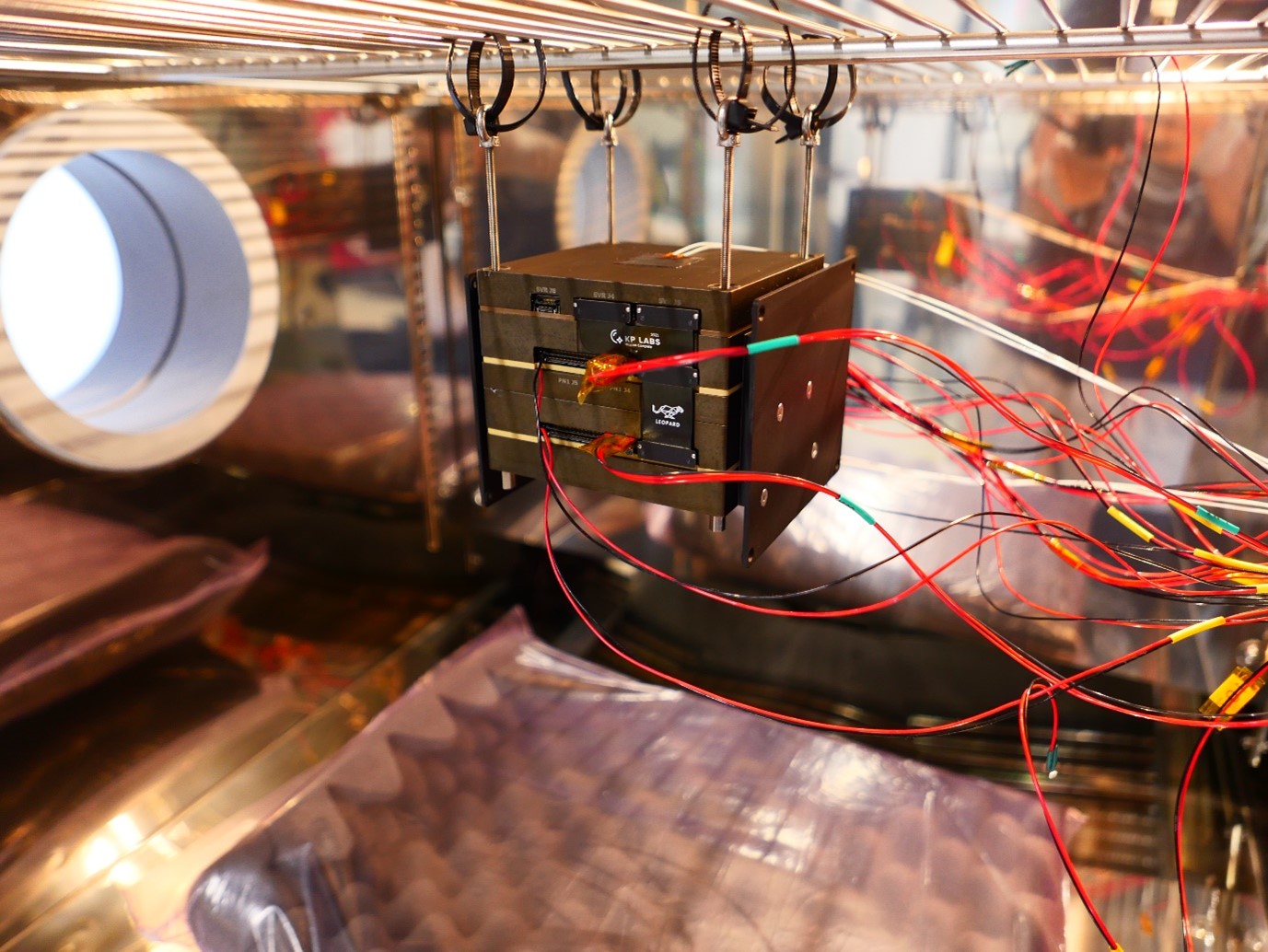
Leopard DPU during thermal test in KP Labs’ climatic chamber.
Critical Evaluations Post-Integration
Following the full integration of the Intuition-1 Spacecraft, several critical evaluations were conducted. A Thermal Vacuum (TVAC) test was deployed to validate the operational efficiency of the thermal control system under vacuum conditions and to ensure the electronic components functioned across varying temperature ranges. The RF anechoic chamber was employed to ascertain the performance of radios and antennas. Ultimately, the spacecraft was subjected to a vibration table assessment to verify its resilience against the rigorous conditions of a rocket launch.
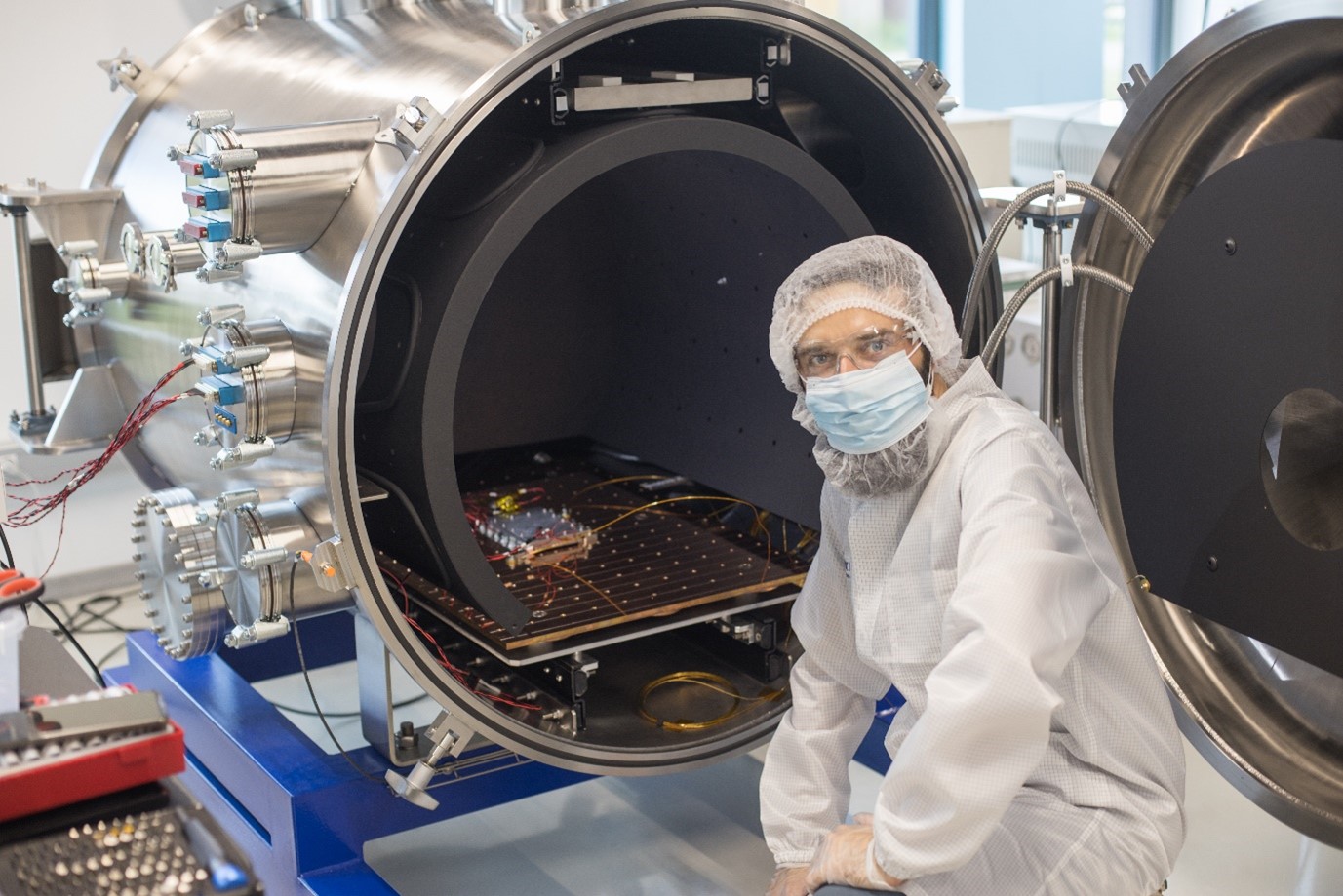
Preparing Leopard DPU for a test in KP Labs’ TVAC.
TVAC Tests
Performed TVAC tests covered Survival and Operational test scenarios. During that test the Spacecraft was experiencing the temperature range from -20°C to + 50°C, while the chamber pressure was set to 10⁻⁵ mBar. During different phases of the TVAC test scenario, different all the components were put in different states – e.g. Leopard was put in idle, image acquisition and Machine Learning processing states. We can confidently state that the entire test cycle, spanning six days, proceeded without any complications.
Radio Testing and the RF Anechoic Chamber
Performing the functional tests on the ground usually happens via a cable connection with the spacecraft – for both convenience and performance reasons. However, that’s not the way operators are going to communicate with the spacecraft once it is already out there on a low Earth orbit. Therefore, at some point, it is crucial to perform as much radio testing as possible.
Previously highlighted was the unique venue for conducting radio tests: the “RF anechoic chamber.” Analogous to a music recording studio, but tailored for radio waves instead of sound waves, this chamber ensures that electromagnetic radiation isn’t reflected off its walls. This creates a meticulously controlled radio environment. The chamber’s walls, constructed of carbon-compound pyramids, absorb all incoming radio signals. Consequently, every detected signal is guaranteed to be direct, undistorted by reflections or interference from surrounding signals.
An essential aspect of the chamber is its ability to insulate against external signals, effectively simulating the profound silence of space and facilitating satellite-ground station communication. This chamber was instrumental in verifying the performance of all communication systems on board, encompassing UHF, GPS, S-band, and X-band frequencies.
To delve into specifics: for uplink signals, the focus was on measuring the requisite power for accurate data reception by the spacecraft. Conversely, for downlink signals, the emitted power from the spacecraft was gauged. Ensuring these measurements requires a controlled radio environment and finely calibrated antennas. By juxtaposing the measurements against the anticipated theoretical values, it’s feasible to evaluate the spacecraft’s overall performance influence and confirm the harmonious operation of all integrated components.
Regarding radio communication for Intuition-1: KP Labs will leverage the Ground Station strategically located atop our Gliwice HQ. This station is proficient in operating across UHF, S-band (uplink), and X-band (downlink) frequencies!
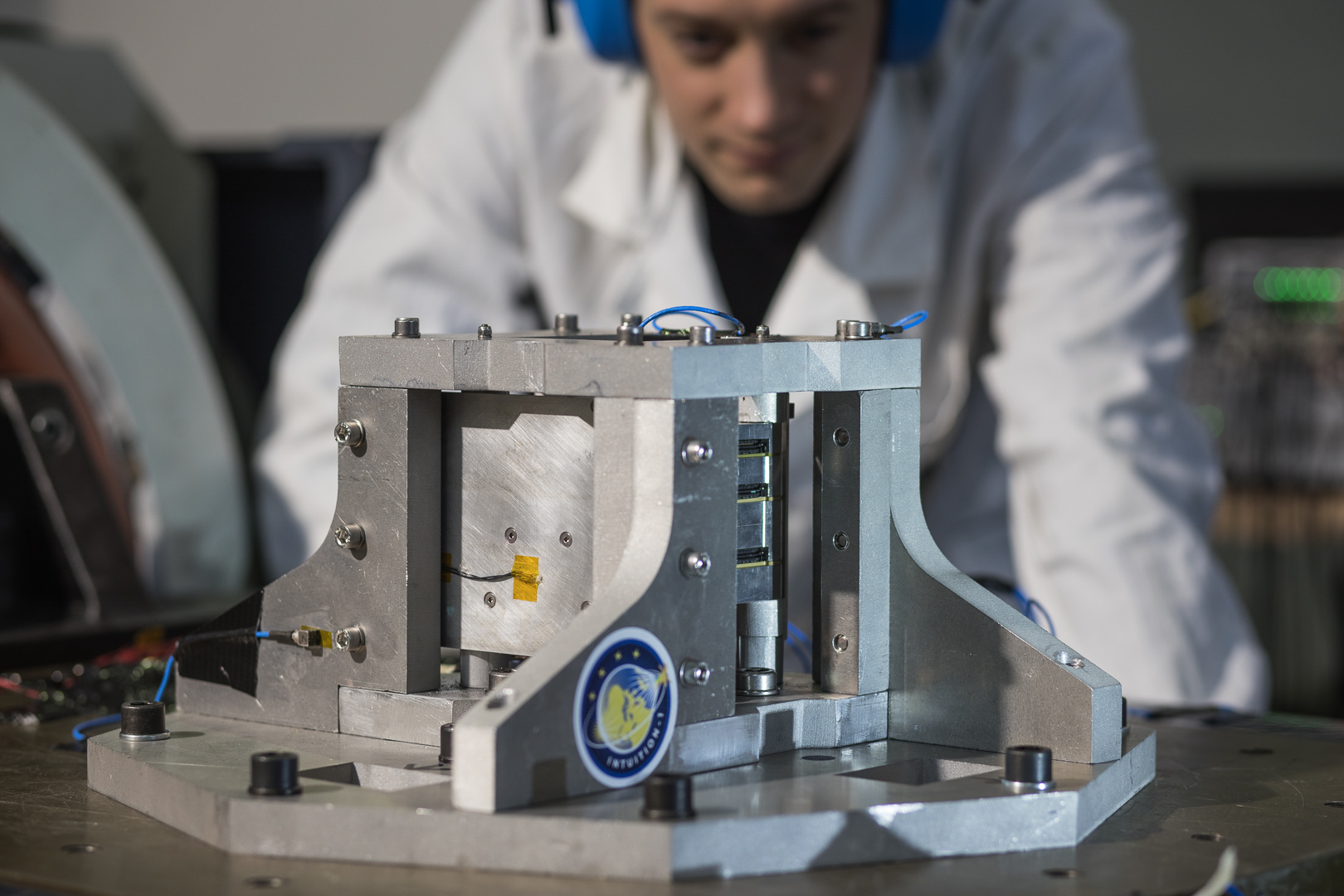
Leopard DPU during its vibe test.
Vibration Test
The final test, which was the most high-risk, was the vibration test. This one has one simple purpose – to prove that not only Spacecraft will survive the rocket launch but also it will not lead to the damage of neighboring payloads. While there are industry benchmarks stipulating test levels, the specific test criteria are typically set by the Launch Provider for each individual flight.
In our case, test Levels were determined by both Deployer manufacturer and Falcon-9 requirements, making them a little higher than standard Falcon 9 test levels from RPUG. We used a wide range of frequencies — from a mere 0.016 g2/Hz at 20 Hz to a robust 0.045 g2/Hz at high frequencies like 150 Hz. Even at the daunting 800 and 925 Hz levels, it stood firm with 0.036 g2/Hz.
Post-Testing: System Assessments and Software Integration
Upon concluding all environmental tests, we executed a comprehensive functional assessment to ascertain the integrity of all Spacecraft subsystems, and it was gratifying to confirm their optimal performance. Intuition-1 employs software powered by the Oryx SDK for satellite platform management. Throughout terrestrial evaluations, the Oryx SDK rendered seamless oversight of the satellite platform’s status and operations. Its capability to run scripts onboard further empowered the integration team to tailor test protocols, assuring the platform’s robustness. The SDK, enriched with Python-based tools, seamlessly melded with Jupyter Notebooks, allowing the creation of automated, interactive notebook testing procedures by the integration team.
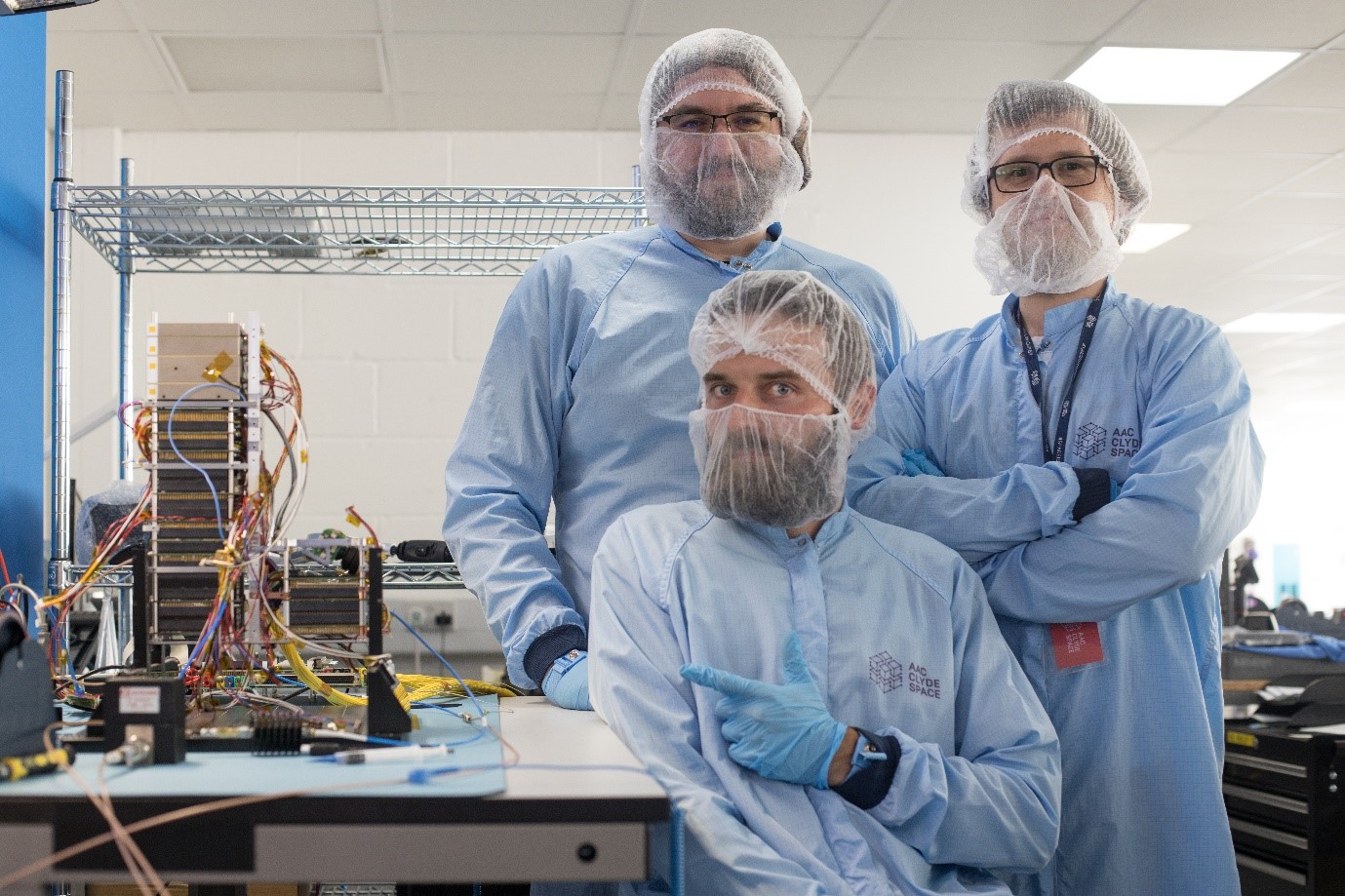
KP Labs’ team, after successful integration of Leopard DPU with Spacecraft bus, image courtesy of AAC Clyde Space.
Spanning two months, the AIVT campaign commenced with the delivery of KP Labs’ components to AAC Clyde Space HQ and concluded as the fully integrated Spacecraft was prepped for transport to the launch site. Thanks to the great experience of both companies we managed to successfully deliver the Spacecraft that is going to be launched NET November this year!
More news
Stay informed with our latest blog posts.